Empowering tomorrow’s solutions through innovation
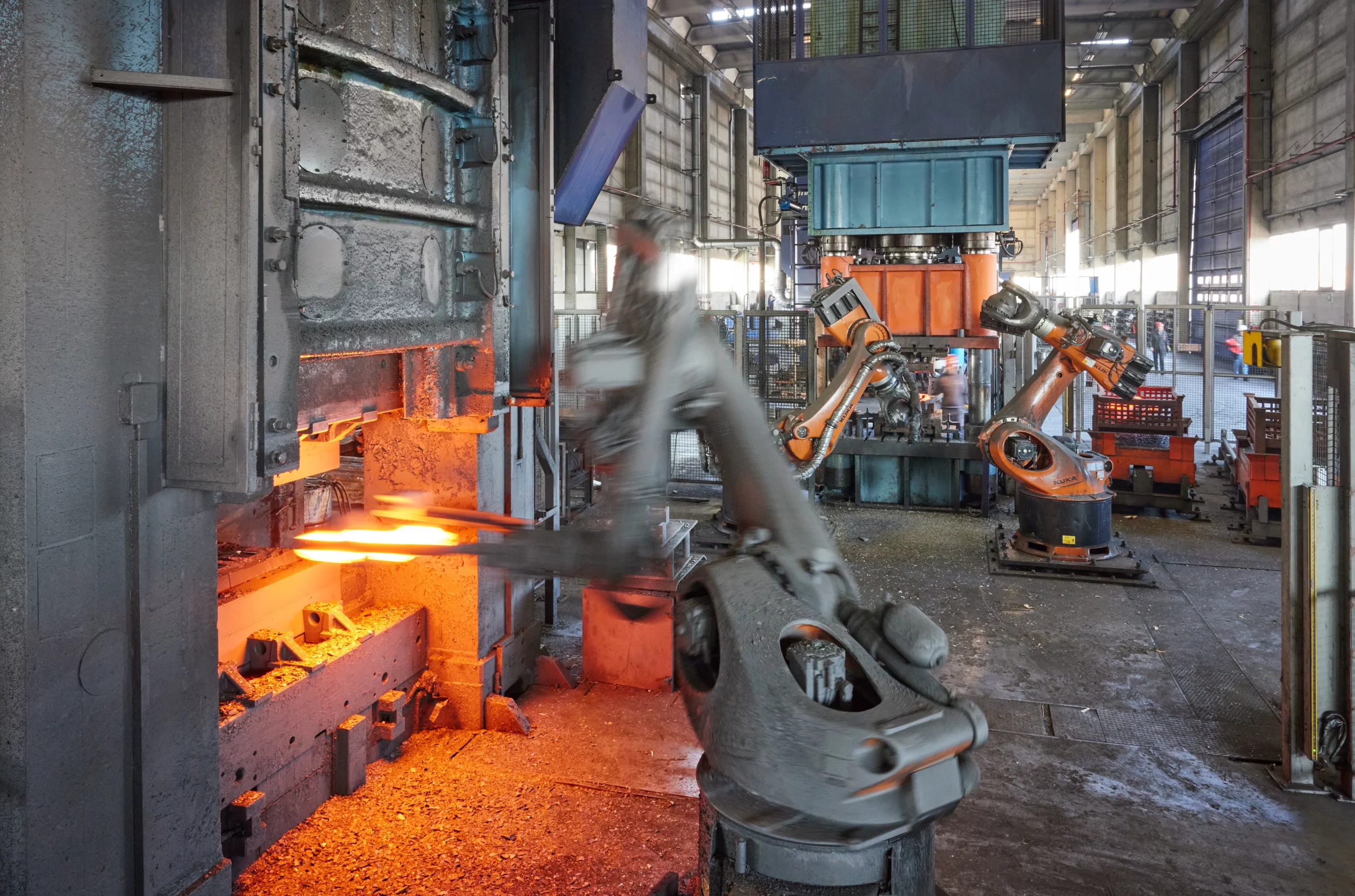
Investing in technology means prioritizing the quality of production, ensuring the safety of our staff, and fostering the growth of our company: investing in technology means investing in the future. We firmly believe that research and development are indispensable to stay abreast of an ever-evolving market, ensuring we remain competitive and innovative.
Our aims have always centered around maintaining control over every stage of production, from the design to the finished part, thereby reducing time-to-market and delivering tailor-made solutions to any customer. We take pride in the increasing international recognition of our pursuit of excellence, as evidenced by influential companies continually reaffirming their trust in us.
We have powerful software capable of handling the entire production cycle. Therefore, we can predict the feasibility and final results as early as the offer stage, thus improving efficiency in subsequent production stages. All applications running on the machinery for die engraving, as well as on CNC centers, are CAD-CAM generated to allow maximum flexibility.
We design and produce both the forging dies and the machining tools needed to obtain the finished part in full autonomy. Our dies construction workshop is equipped with 9 machining centres and 2 CNC lathes capable of engraving moulds suitable for our presses up to a maximum size of 1300 mm x 550 mm x 400 mm high and 550 mm on round moulds.
We have 6 lines for hot forging, 3 of which are robotized, equipped with mechanical presses from 1,600-ton up to 8,000-ton which allow us the production of parts weighing from 0,1 up to 180 kg in steel, and from 0,5 up to 40 kg in aluminum alloys: the greatest flexibility to meet the most various types and design needs.
We possess furnaces capable of solubilizing duplex, super duplex, and stainless steels, as well as conducting treatments on exotic alloys. We work together with qualified suppliers for the heat treatment of carbon and alloy steels.
Our in-house destructive testing laboratory, compliant with ISO / IEC 17025: 2017, ensures the prompt analysis of the mechanical properties achieved after treatment. It is also equipped with a tensile testing machine and two pendulum impact testing machines to meet the requirements of both EN and ASTM standards, a spectrometer, a microscope, and a durometer.
Our mechanical machining department is in continuous evolution, currently boasting forty CNC machines, including multitasking centers, vertical and horizontal working centers. Having invested throughout the years on the best industrial machinery available on the market, we can guarantee accuracy and precision in every type of mechanical machining.
We have dedicated a building, equipped with 6 benches for magnetic particle inspection and 1 semiautomatic line for dye penetrant inspection and 1 line for color contrast PT method, to non-destructive testing in order to verify the integrity of parts after forging and heat treatment. All our control operators are qualified to ISO 9712 level II standards.
Superficial treatment, or surface treatment, refers to a range of processes applied to the surface of a metal to enhance its properties, such as appearance, corrosion resistance, hardness, and wear resistance. These treatments are essential in various applications to improve the performance and longevity of metal products.
Before any component is approved for distribution, it undergoes rigorous testing and inspection. This phase ensures that each piece meets the highest standards of precision, strength, and safety. We have metrology room equipped with three coordinate measuring machines and a 3D laser scanner for dimensional checks on both raw and machined parts. It is through these rigorous procedures that we can guarantee a finished product of impeccable quality.
Each item is carefully packaged using high-quality materials that provide adequate protection during transit. Our packaging process is designed to minimize the risk of damage and ensure that products arrive intact and ready for use. We prioritize customer satisfaction and strive to provide a seamless experience from order placement to delivery.